Articles & News
Exploring the Spectrum: Your Guide to Apparel Printing Ink Types
When creating eye-catching and vibrant custom apparel, choosing the type of ink used is crucial in dictating the final print results. In this guide, we’re taking an in-depth look at the spectrum of ink types we offer and exploring the diverse print outcomes.
April 2nd, 2024
Exploring the Spectrum: Your Guide to Apparel Printing Ink Types
When creating eye-catching and vibrant custom apparel, choosing the type of ink used is crucial in dictating the final print results. In this guide, we’re taking an in-depth look at the spectrum of ink types we offer and exploring the diverse print outcomes.
April 2nd, 2024
5 Ways to Elevate Your Brand with Threadbird
Are you a business owner looking to take your brand merchandise to the next level? Well, you have come to the right place! Threadbird's decoration services offer a plethora of options & styles to elevate your products and make them truly unique. We're sharing five ways that we can help you level up your brand merchandise game.
February 15th, 2024
Threadbird's Tailored Touch: Power of Product Customization
Dream, design, and invent products like no other, through Threadbird’s cut & sew program. In this blog, we’re taking a closer look at the creative possibilities for customization by showing you some of our favorite custom products.
February 1st, 2024
Articles & News
Brand Feature: Threadfast, an Eco-Friendly Brand
The Fashion Industry isn’t typically the first thing that comes to mind when you think about pollution. Our minds usually draw to more obvious things like gas and chemical pollution. But, the garment industry has its own history of contributing to the issue.
April 29th, 2020
Exploring the Spectrum: Your Guide to Apparel Printing Ink Types
When creating eye-catching and vibrant custom apparel, choosing the type of ink used is crucial in dictating the final print results. In this guide, we’re taking an in-depth look at the spectrum of ink types we offer and exploring the diverse print outcomes.
April 2nd, 2024
5 Ways to Elevate Your Brand with Threadbird
Are you a business owner looking to take your brand merchandise to the next level? Well, you have come to the right place! Threadbird's decoration services offer a plethora of options & styles to elevate your products and make them truly unique. We're sharing five ways that we can help you level up your brand merchandise game.
February 15th, 2024
Threadbird's Tailored Touch: Power of Product Customization
Dream, design, and invent products like no other, through Threadbird’s cut & sew program. In this blog, we’re taking a closer look at the creative possibilities for customization by showing you some of our favorite custom products.
February 1st, 2024
Subscribe to our Newsletter!
Lorem ipsum dolor sit amet, consectetur adipiscing elit, sed do eiusmod tempor incididunt ut labore et dolore.
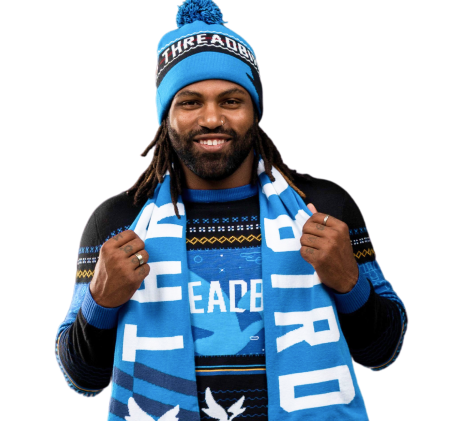